Introducing Training and Development Tax Credits
Written by: Andrea Wilson
1 min read
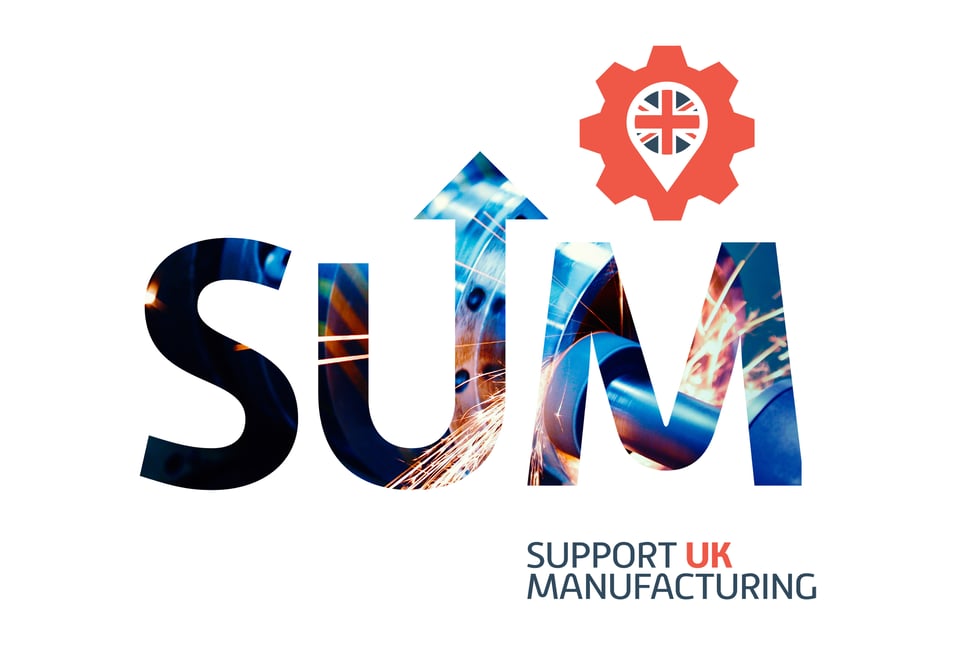
We have submitted our idea as to how a T&D Tax Credit system could work, including demonstrating how this could demonstrate a clear “Value for Money” benefit to Government.
Join in on the conversation on LinkedIn
Follow Andrea Wilson on LinkedIn for all the latest updates with the Support UK Manufacturing campaign.
Andrea Wilson is a successful and passionate company Director (Hone-All) with a wide range of skills, experience, and responsibilities within business and in general within the Engineering & Manufacturing Industry.
Andrea has a burning passion for engineering and manufacturing and is constantly working to improve the image and support for UK manufacturing. Andrea campaigns for better quality training provision; for Government support which suits a wider variety of business sizes and specialities; and also improving the recognition and image of engineering and manufacturing within the UK.
An alternative way of bridging the skills gap
Support UK Manufacturing are suggesting an alternative way of bridging the skills gap currently being faced at a manufacturing production level which would not only assist in raising the levels of technical sills within the UK, but also enhance productivity as currently unskilled workers will become skilled, productive and "earn whilst they learn".
Our suggestion would deliver rapid results, in a practical, easy to administer and effective way, to help bridge the skills gap, drive a broader up-skilling of the workforce, improve productivity, and encourage companies to train at a companies are reluctant to train due to risk of poaching.
We call this Training and Development (T&D) Tax Credits.
Training and Development Tax Credits
Most colleges cannot provide the quality and variety of training and skills needed due to either not having the appropriate equipment, or those who are lucky enough to have the equipment cannot find suitably qualified personnel to train others upon it.
We propose that businesses create their own syllabus of applicable skills which would include every functional aspect of the business including Administration, Goods In, Production, Inspection and Despatch. These would be called Internal Apprenticeships or In-company Apprenticeships.
The course could be based on current training matrices within the business (which most businesses have, but if not, could be available in a central portal) and includes varying levels of training. For example, in terms of machinery, these could include - Trained to Run, Trained to Set, Trained to Part Program, Trained to Program, Fully Experienced.
Alternatively, companies are provided with a template syllabus, with room for modular variation, so that a proportion is tailor-made to the business, which would enable specialist training to be delivered, as well as the more generic skill sets.
These are signed off by engineers/qualified personnel on a weekly or monthly basis and then audited by representatives from the local colleges who will request demonstrations of the skill levels achieved. If these are not available, companies signed up to the scheme could be asked to donate a member of qualified personnel for a number of hours per week to go an audit the quality of the training in other local businesses.
The hours clocked against these training activities, i.e. the tie spent by engineers training them, would be recorded on Time Sheets as we do currently when declaring a percentage of their time spent on R&D activities.
Any materials and tooling lost as a result of the training could potentially be included.
These hours and/or losses are then calculated, and a percentage claimed back from Corporation Tax due.
Permitting this type of training would not only ensure that the engineers are trained in the types of skills we need, on the machinery we use, but by engineers who are already qualified and trained not just in the "skill set" required, but also the quality standards and business ethos.
If some of the skills are not transferrable locally, these could be paid at a lower percentage reclaim rate. For those which are transferrable, i.e. admin, CNC turning, programming, inspection etc, could be claimed at a high level.
If practical tests were brought in to qualify for higher/degree level manufacturing qualifications, the internal qualifications obtained could then be used to satisfy entry requirements.
This scheme would not only apply to school leavers but could also include any age and any level, including the longer term unemployed and ex-service personnel.
Colleges would no longer have to invest in capital equipment. Productivity increases, skills gaps are addressed, companies have employees trained internally so are fully skilled and also embedded within the business and its culture by being a Tax Credit.
The only way a Government contributes is as and when the business is profitable.